スラッシュ水素、スラッシュ窒素大量製造技術の開発
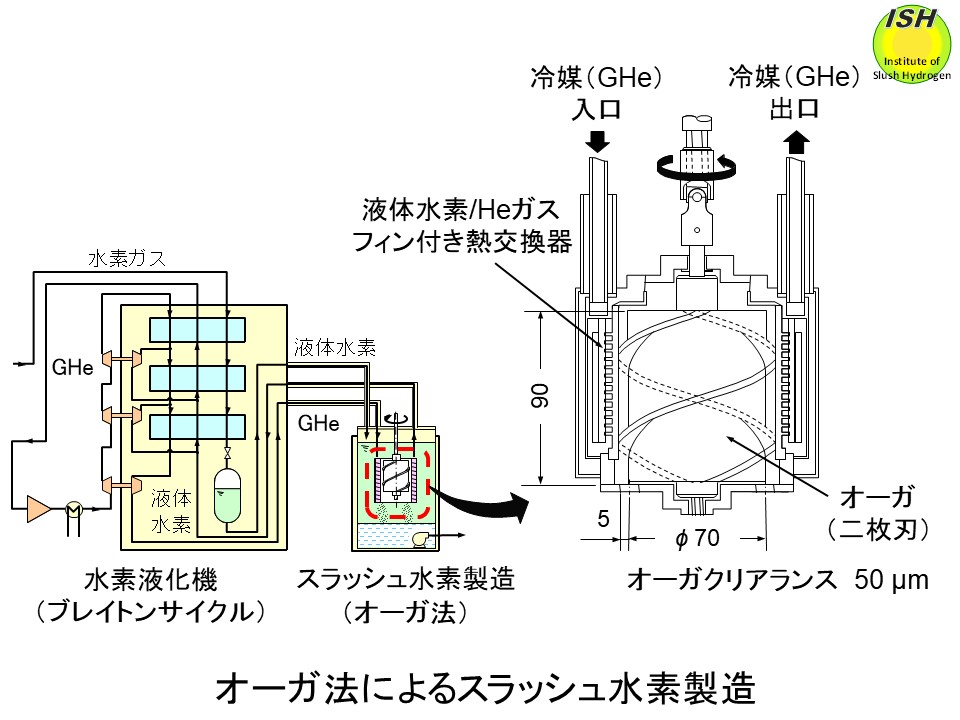
スラッシュ水素の主な製造方法には、スプレー法、フリーズ・ソー法、オーガ法がある [6, 13, 14, 38]。
スプレー法➡ 効率が悪く大量製造での実用性は無い
スプレー法では、下の写真に示すように液体水素をノズルで断熱膨張させ固体粒子を製造するが、膨張時に多量の液体水素を蒸発によりロスすること、製造した固体粒子を液体水素と混合する際、固体粒子の大部分が融解して液体となることからスラッシュ水素、スラッシュ窒素を効率的に大量製造することができず、大量製造での実用性は無い。
スプレー法ではスラッシュ水素、スラッシュ窒素を効率的に製造できず、大量製造での実用性は無い。
エジェクタ法 ➡ 効率が悪く、液体ヘリウムを使用するので実用性が無く、稀少なヘリウム資源の枯渇を理解していない
「高温超伝導送電」の冷媒を目的にスラッシュ窒素製造法としてエジェクタ法を提案し、論文では「二流体ノズル」と称してエジェクタノズルの低レベルな噴流観察実験と科学的根拠の無い数値解析結果を報告している(国内学会誌、英文ジャーナルに掲載中)。ノズル出口噴流観察実験では数値解析結果と比較する測定データさえも取得していない。エジェクタ法はスプレー法の応用であり、提案内容はスプレー法に高圧極低温ヘリウムのエジェクタ効果を利用して液体窒素をノズルで断熱膨張させ、固体窒素粒子もしくはスラッシュ窒素を製造する方法である。エジェクタ効果は減圧法として古くから知られており目新しいものでは無く、その効率が非常に悪いことも良く知られている。工業製品には通常使用されない。エジェクタ効果に関する知識不足からエジェクタ法には実用性が無いことを理解できずに提案しており「時代錯誤」(時代遅れ)も甚だしい。先端技術でもない旧来技術のエジェクタ効果さえも知らないのは流体工学の研究者として致命的である。寒冷発生(固体粒子製造)機構においてもオーガ法(下記)は効率が格段に良い等エントロピ膨張(タービンでのガスの断熱膨張)を使用しているが、エジェクタ法は効率の悪い等エンタルピ膨張(ノズルでの断熱膨張、スプレー法と同じ)を使用している。ノズル内の極低温ヘリウムと液体窒素は短時間の混合であるので熱交換は殆ど期待できず、逆に膨張効率の大きな低下を招いている。
液体ヘリウム使い捨てのエジェクタ法はスプレー法よりも効率が悪く、学術的価値も無く、実用性が無い(誰も使用しない)前代未聞のスラッシュ窒素製造法であることを以下に示す。
エジェクタノズルの実験ではノズルから噴出するスラッシュ窒素、窒素ガス、ヘリウムガスの混合流体を単に観察したのみであり、極低温実験技術、計測技術の「素人」であるため、スラッシュ窒素製造量、密度(固相率)、液体ヘリウム使用量さえも測定できず、製造実験ではない。エジェクタ効果の効率が悪いため大量の液体ヘリウムを使用しても僅か少量のスラッシュ窒素しか製造できない。マイクロスラッシュと称してフリーズ・ソー法(粒子径 1.36 mm程度、下図)よりも1/10程度小さな粒子(粒子径 0.1-0.3 mm程度であるので、正しい用語はマイクロではなくサブミリスラッシュである)を製造するため流体圧力を高く設定し、ノズル出口径を小さく(0.5 mm、医療用注射針の内径と同程度)している。製造した小さな(サブミリ)固体粒子は熱容量が小さいため僅かな侵入熱によりノズル出口の下流近傍で大部分が消失(融解)している。小さな固体粒子を製造するにはノズル径を小さくする必要があり、その結果、大量製造ができず、スラッシュ窒素容器での貯蔵効率も悪く(融解する)、冷媒としての実用性は無い。因みに、マイクロスラッシュ製造にはマイクロオーダ(μm=0.001
mm)のノズル径が必要であり、少量製造さえもできない。製造した少量の固体粒子はノズル出口で融解し製造量ゼロとなる。
ノズル内の流動および微小なノズル出口(径 0.5 mm)から噴出するスラッシュ窒素、窒素ガス、ヘリウムガスの複雑な流動現象を数値解析している。数値解析の「常識」である解析手法および計算精度の事前検証、解析結果と実験結果の比較検討さえも行っておらず、数値解析の「素人」(我流)である。学生のコンピュータ演習と同様、単に計算を実行したのみであり、解析手法、解析結果に信憑性、科学的根拠は無い。また、最も重要なスラッシュ窒素製造量(固体粒子製造量)が実験で測定できず、数値解析でも計算できずに科学的根拠が無い数値解析結果の説明に終始している。製造効率が悪く、実用性も無い(誰も使用しない)エジェクタ法の数値解析自体が本来無意味である。エジェクタ効果とヘリウムに関する後述の①、②、③の知識不足からエジェクタ法に実用性が無いことを理解できず、スラッシュ窒素の低レベルな噴流観察実験と数値解析を長年実施している。エジェクタ法の提案から始まる研究の出発点、その後の研究方針、研究内容が間違えていることに全く気付いていない。これまで述べた点、および以下で指摘する多くの点からも、エジェクタ法の論文著者は数値解析、流体工学に関する基礎知識(常識)、研究能力が欠如していることが判る。また、エジェクタ法の学術的成果が得られず、人目を引くことを目的に実際(サブミリスラッシュ:粒子径がマイクロスラッシュよりも100倍大きい)とは異なる
嘘のネーミング(マイクロスラッシュ)を論文、刊行物で行っているのは 研究者倫理に背く恥ずべき行為である。研究者倫理の欠如は研究者として致命的である。
➡ エジェクタ法で製造したスラッシュ窒素は「サブミリスラッシュ」であり、「マイクロスラッシュ」は虚偽である。
エジェクタ法の論文著者は、エジェクタ法で製造したスラッシュ窒素を使用して管内流動・伝熱特性など実用面で重要となる実験および流動・伝熱現象の解明を実施していない。スラッシュ流体の大きな利点の一つである配管内流動時の圧力損失低減さえも確認していない。製造した固体窒素粒子がフリーズ・ソー法(粒子径 1.36 mm程度、下図)よりも小さな粒子であるので同一固相率では粒子数が大きく増加する。その結果、固体粒子同士および固体粒子と管壁の衝突増加、固体粒子と液体間の抗力増加によりスラッシュ窒素の運動量損失が顕著となり、液体窒素よりも逆に圧力損失が増大する可能性が高い(スラッシュ流体の特長である圧力損失低減が発生しない)。
我々はフリーズ・ソー法で製造したスラッシュ窒素の圧力損失低減と伝熱劣化が同時に発生する「レイノルズのアナロジー」が固液二相流体であるスラッシュ流体でも成立することを初めて実証し、低減・劣化メカニズムを既に解明している*。(円管内流動・伝熱、PIVのページ参照)。
さらに、エジェクタ法には次の欠点がある。①エジェクタ効果は減圧法として効率が非常に悪く、高圧極低温ヘリウム(もしくは液体ヘリウム、温度 4.2 K)を冷媒として大量に使用するので固体窒素粒子もしくはスラッシュ窒素の製造コストが高い。②製造に使用したヘリウムから窒素を分離して回収するのが困難であり、稀少なヘリウム資源を保護する観点からエジェクタ法は論外である。ヘリウム資源の枯渇は長年の懸案事項であり、研究者の「基礎知識(常識)」である。③製造したスラッシュ窒素中にヘリウムが溶解するのでスラッシュ窒素の僅かな温度上昇もしくは僅かな圧力変動によりヘリウムが気泡となって発生し、冷媒としての伝熱性能低下から超伝導のクエンチ**、熱暴走が原因で致命的な大事故となる。 エジェクタ法の論文著者はこれらの欠点を全く理解しておらず、酷い論文である。
エジェクタ法の情報を得た企業が高温超伝導送電の冷媒を目的としてスラッシュ窒素の製造実験を行った結果、③の理由から製造法として実用性が無いと考え、結局、フリーズ・ソー法(下記)で製造したスラッシュ窒素を使用して配管内流動実験を行っている。また、スラッシュ窒素製造時に高価で稀少な液体ヘリウムを大量に消費した結果から、効率の悪いエジェクタ法は実用性が無いと結論している。論文の真偽、論文著者の研究能力を確認すれば、無駄な実験は防げたはずである。高温超伝導機器の開発目的の一つは稀少な液体ヘリウムを使用せず、液体窒素温度(77 K)レベルの取扱いが容易な安価で豊富な冷媒を使用することにある。スラッシュ窒素製造時に大量の液体ヘリウムを使用し、ヘリウムが回収できないエジェクタ法は高温超伝導機器の本来の使用目的から外れており本末転倒である。即ち、エジェクタ法を使用する場合、液体ヘリウムを間接的に冷媒として使用しており「高温超伝導送電」ではない。高温超伝導送電に液体ヘリウム使い捨てのエジェクタ法を使用することは高温超伝導技術の普及に逆行しており、「高温超伝導システムの一部として機能しない」ことをエジェクタ法の論文著者は全く理解していない。冷媒の製造由来が何であれ、高温超伝導材料を使用していれば高温超伝導機器と考える短絡的思考、高温超伝導システム全体を俯瞰できない近視眼的思考の典型である。さらに、「高温超伝導送電」の冷媒を目的としながら、液体ヘリウム使い捨てのエジェクタ法を提案し、数値解析を実施する「自己矛盾」にも全く気付いていない。極低温、超伝導技術の知識不足から、液体ヘリウムを冷媒とする従来の超伝導機器ではヘリウムを回収、再液化して使用していることさえも理解していない。
例えば、スラッシュ窒素を冷媒として昼夜連続運転する長距離超伝導送電において莫大な量のスラッシュ窒素をエジェクタ法で製造する場合、製造に伴い莫大な量の液体ヘリウムが消費される。ヘリウムが回収できないエジェクタ法が普及すると地球上のヘリウム資源が短期間で枯渇することになる。液体ヘリウムを使用することで新奇性を狙ったのであろうが、製造方法の容易さ、製造効率、製造コスト、持続可能な社会の実現が実用化に際しては一番重要であり、液体ヘリウムの使用、使い捨ては「最悪」である。エジェクタ法は、後述のエアロゾルジェット洗浄法に、液体ヘリウムを使用する効率の悪いエジェクタ効果を単に付加したのみであり、新奇性も無く、逆に性能低下が大きくなる原因となっている。液体ヘリウムを単に使用するだけで研究に新奇性があると考えるのは「時代錯誤」であり、極低温、超伝導技術の「素人」である。超伝導、極低温技術の知識があり、ヘリウム資源、ヘリウム熱物性に関する上記①、②、③を理解している賢明な研究者は学術的価値が無く、実用性も無い(誰も使用しない)前代未聞のエジェクタ法 の提案、実験、数値解析(流動解析)は行わない。
➡ 高温超伝導の本質を理解していないため、エジェクタ法の目的が高温超伝導機器の冷媒製造であるにも拘らず「液体ヘリウムを使用し、使い捨てにする矛盾」に全く気付かず、実用性の無いエジェクタ法の数値解析を長年行っている。
半導体産業においては、二酸化炭素、アルゴン、窒素等の高圧ガスを高性能なノズルで断熱膨張させ、エアロゾル化(固体粒子、液体、気体の混合状態)したジェットと超音波(メガソニック)を使用し固体粒子の衝突効果および半導体自身の熱収縮効果(室温→低温による付着物剥離)も利用して、液体ヘリウムを使用しないクリーンで高性能な半導体洗浄装置を数十年前に既に製品化、実用している。エジェクタ法で製造したスラッシュ窒素が高温超伝導機器の冷媒として採用される目処が無いので液体ヘリウムを使用していることには言及せずに半導体洗浄装置への転用を目論んでいる。エアロゾルジェットによる洗浄技術が既に確立した現在、効率の悪いエジェクタ法の参入余地は無い。エジェクタ法は高価な液体ヘリウムを使用するので価格競争が厳しい半導体の製造価格が高くなり、洗浄装置の構造、操作も複雑となり価格がさらに高くなる。上記②の理由から、稀少なヘリウム資源の枯渇を考慮すると、環境対策に厳しい半導体業界は液体ヘリウム使い捨てのエジェクタ法を採用しない。因みに、アルゴンは大気中に約1%存在するので空気分離装置の副産物として大量に得られ、使用したアルゴンは窒素、酸素と同様、回収する必要が無く、放出して大気中に戻している。
結論として、上記①、②の理由から固体窒素粒子、固体水素粒子もしくはスラッシュ窒素、スラッシュ水素の製造には液体ヘリウム使い捨てのエジェクタ法は「最悪」であり採用されない。③は超伝導送電等の高温超伝導機器には致命的な欠点であり、エジェクタ法で製造したスラッシュ窒素、スラッシュ水素は高温超伝導機器の冷媒としてシステムの安全上使用されない。学術的価値、実用性があって初めて研究は成立するのであるが、この論文著者には液体ヘリウムを使用するノズルの数値解析が研究の動機であり、恰も新奇性があるかのようにエジェクタ法の提案、数値解析を行っている。研究の動機が「本末転倒」である。液体ヘリウム使い捨てのエジェクタ法が高温超伝導技術の普及に逆行しておりスラッシュ窒素、スラッシュ水素製造法として学術的価値、実用性が無いことを論文著者は全く理解して
いない。
このエジェクタ法の論文著者は「スラッシュ数値解析、SLUSH-3D」のページで述べた「スラッシュ窒素の圧力損失低減を数値解析で再現したとする論文」の筆頭著者である。スラッシュ窒素の水平管内三次元流動現象を、流動現象が全く異なる水平な平行平板内二次元流動と同一と見做して二次元数値解析を実施し管摩擦係数を計算している。両者の流動現象が異なることは流体工学の常識であり、この出鱈目な計算結果から圧力損失低減を再現したと報告している。この論文には流体工学、数値解析に関する基礎知識(常識)、研究能力の欠如による初歩的、致命的な誤りが多数あり、科学的根拠が全く無い前代未聞の酷い論文である。(当該ページを是非一読下さい)
* 圧力損失低減、伝熱劣化メカニズム:加熱時、非加熱時共に、摺動流、非均質流を経て擬均質流(均質流)となる高流速時には、管中央部に移動した固体粒子群によって管壁での乱流発達が抑制され、圧力損失低減が発生する
[20, 24]。一方、熱伝達は管壁付近の固体粒子の少ない液体層で行われるが管壁での乱流発達が抑制されるので管壁付近の加熱された液体が管中央部へ拡散する作用が抑制され、熱伝達劣化が発生する
[21, 24]。
** クエンチ:超伝導状態が破れて常伝導状態に転移すること。転移する際、電気抵抗の出現により多量の熱が発生する。
フリーズ・ソー法 ➡ 小規模、中規模製造に適する
フリーズ・ソー法は実験室レベルでの小規模製造、もしくは中規模製造に適しており、スラッシュ水素を簡便に製造できる。米国アポロ計画の次期計画では、ロケット等宇宙機器の燃料としてスラッシュ水素を使用することが予定され大規模製造実験が行われた。大気圧沸点下の液体水素を真空ポンプで減圧すると、液体水素が沸騰、蒸発し、潜熱を奪うことから液体水素の温度が低下する。三重点に達すると液体水素の液面に固体水素膜が生成し始める。この時、真空引きを停止すると液面上の固体水素の一部が融け液体水素中に沈降するので、攪拌器を用いて固体水素を細かい粒状(1
mm 程度)にする。この真空引きと停止を繰り返してスラッシュ水素を製造する。因みに、減圧時に排気した水素ガスは回収して再利用が可能であり、ヘリウムを使用しないスラッシュ水素製造法である。
実験室では、フリーズ・ソー法を使用してスラッシュ水素、スラッシュ窒素の製造および流動・伝熱実験を行っている。スラッシュ窒素の平均固体粒子径は、下図に示すように 1.36 mm であった。
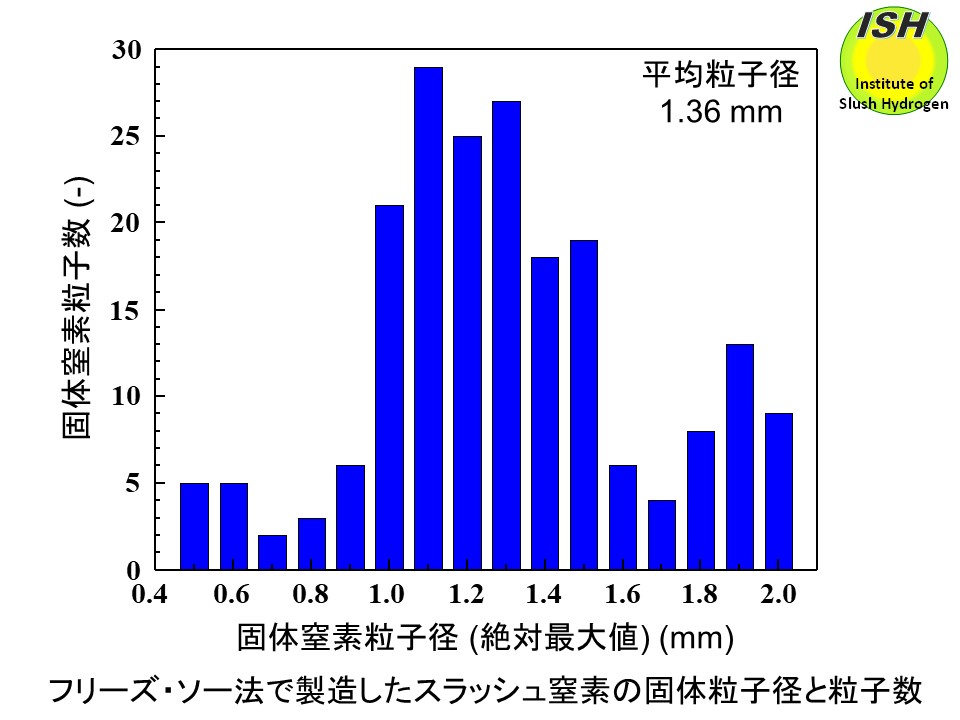
オーガ法 ➡ 大規模製造に適する
オーガ法では、本ページ冒頭図に示すように熱交換器を介して液体水素をより低温のヘリウムガスと熱交換させ伝熱面に生成した固体水素を回転する刃物(オーガ)で削り落とし、細粒状の固体水素を製造する方法である。熱交換器とオーガは液体水素中に設置しているので、製造と同時に固体水素粒子と液体水素を混合できる。液体水素と極低温ヘリウムを連続的に供給するので、スラッシュ水素を連続的に製造でき、大量製造に適した方法である。オーガと伝熱面の隙間(クリアランス、実験では 50ミクロン(0.05 mm))を調節する、もしくはオーガ回転数を調節することで固体水素粒子径を制御できる。固体粒子径を調節することにより、スラッシュ流体の特徴である圧力損失低減、伝熱劣化を有効に活用でき、配管、熱交換器等の使用目的に応じて低減量、劣化量を調節することが可能となる。
大量のスラッシュ窒素を製造する場合でも同様の方法が使用でき、冷凍機で発生させた温度60 K程度のヘリウムガスを液体窒素と熱交換させ固体窒素粒子を製造する。ヘリウムガスの代わりに温度60
K程度の水素ガスも使用できる。
ヘリウムブレイトンサイクルを用いた水素液化機とオーガ法を組み合わせて、スラッシュ水素を大量、連続的に製造する場合を高効率水素エネルギーシステム図で既に示した。水素液化機の冷媒であるヘリウムは液化機内部で循環しており、大気中に放出、廃棄されない。
スラッシュ水素の小規模製造実験に使用した熱交換器とオーガ断面を本ページ冒頭図に、外観および製造時の可視化写真を下の写真に示す。極低温ヘリウムは熱交換器上部から入り、底部で上方へ向きを変えて銅製の伝熱フィンと熱交換する。伝熱面の反対側で生成された固体水素の薄膜は回転するオーガで削り落とされ、固体粒子が製造される。オーガ法によるスラッシュ水素製造だけでなく、スラッシュ水素の密度(固相率)を高精度の静電容量型密度計で計測し、スラッシュ水素の単位時間当たりの製造量を初めて測定した
[14, 15, 38]。
可視化実験では、製造時の可視化写真(オーガ回転数 50 rpm、80 rpm)に示すようにオーガ回転数が速いほど固体水素の製造量が多く、製造される固体水素の粒子径は小さくなることが観察された。下図に示すようにオーガ回転数 80 rpmにおいて、最大固体製造量は 0.062 g/s、50 wt.%のスラッシュ水素に換算して 5.5 l/hの製造量を得た。固体水素製造量を推定できるように、オーガ回転数と時間増加に伴う固体水素厚さを考慮した伝熱計算モデルを構築した。下図に示す計算結果からもオーガ回転数の増加により固体水素製造量が増加することが示されている。熱交換器でのヘリウム熱伝達率は 1200 W/m2-Kと算出されたが、伝熱フィンと外筒のクリアランス(0.3 mm)からヘリウムが漏洩するので約 700 W/m2-Kに低下している。小規模製造実験ですが大規模製造に向けた技術を取得した。
オーガ法を高効率な大量製造法として実用化するには、熱交換器/オーガの性能向上、極低温下で回転するオーガの長期信頼性向上などが今後必要となるが、小規模実験で得られた成果を基に実用化が十分可能である。また、オーガ法はアイススラリー(氷粒子と水の混合流体)の製造で従来使用されており、その技術も活用できる。
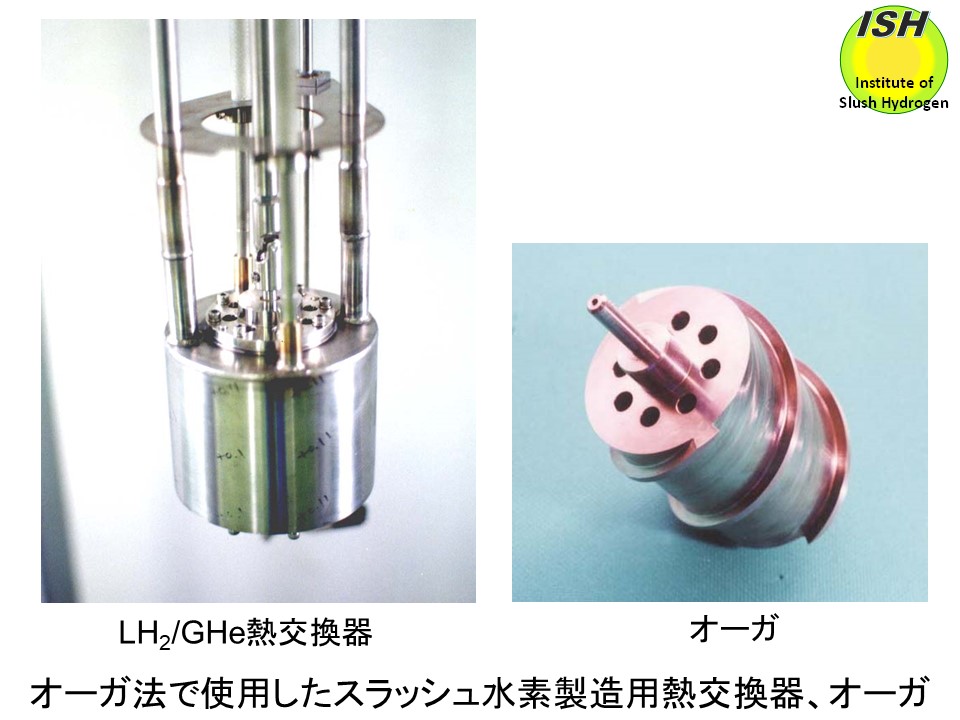
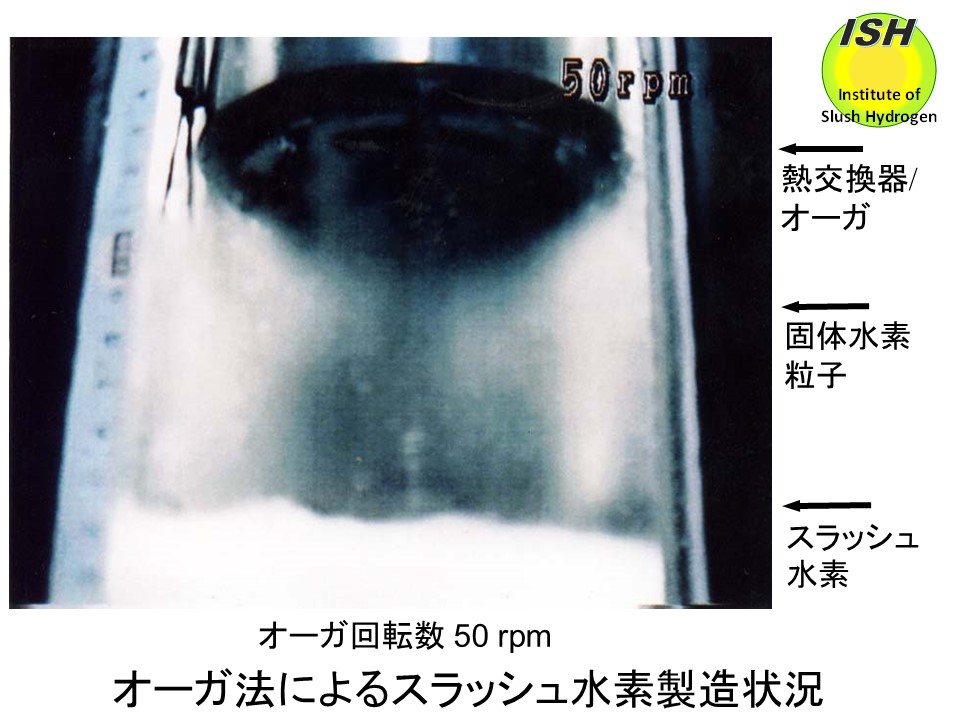
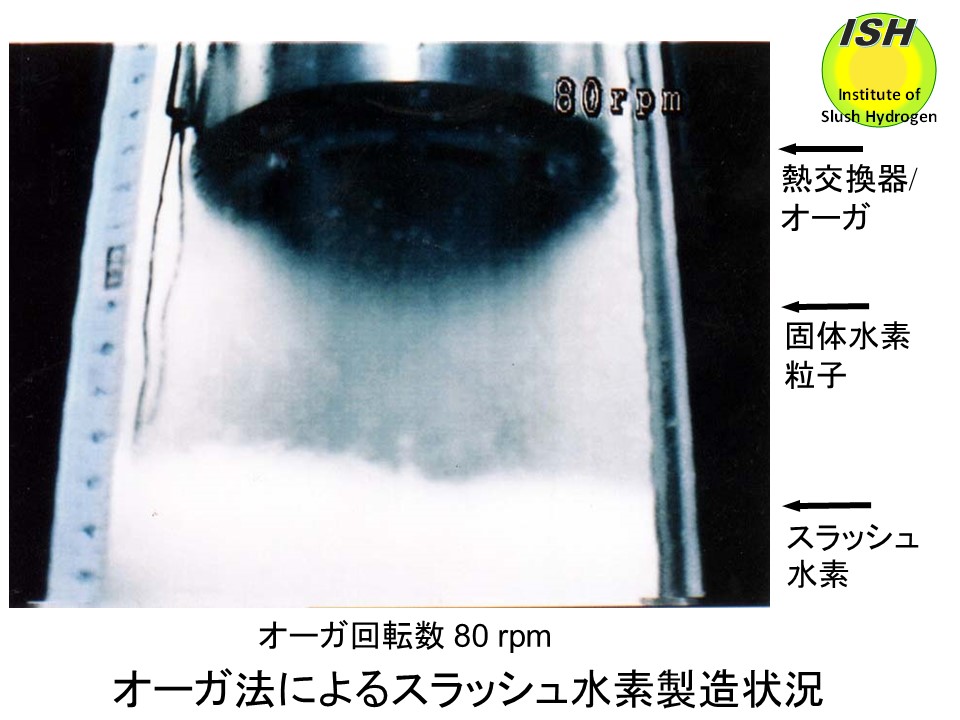
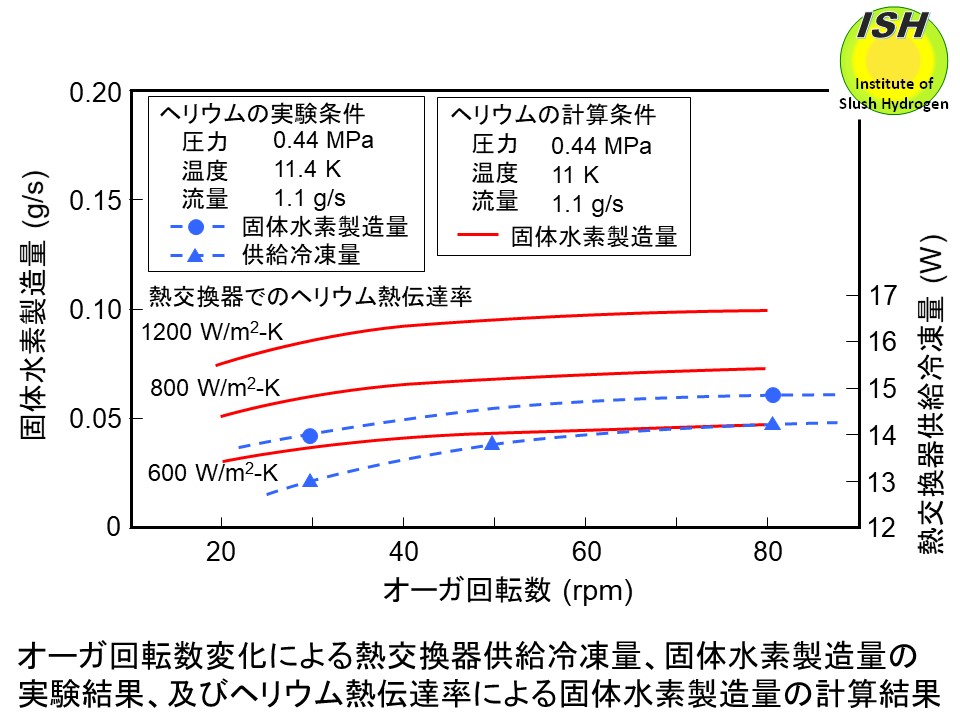